In the field of modern injection molding, hot runner injection molding technology, with its unique advantages, is profoundly changing the production pattern of plastic products and has become a key means for many manufacturing enterprises to enhance their competitiveness.
I. Hot Runner System: Core Operation Mechanism
The hot runner system is the core part of hot runner injection molding processing. It is mainly composed of key components such as the hot runner plate, nozzles, and temperature controllers. The hot runner plate is like a precise "traffic hub", responsible for evenly distributing the plastic melt from the injection molding machine to each nozzle. When the injection molding operation starts, the heating elements quickly operate, continuously supplying heat to the hot runner plate and nozzles, keeping the plastic melt in an ideal molten state within the runner. The plastic melt is like flowing smoothly in an unobstructed "highway", steadily flowing from the injection molding machine nozzle into the mold cavity.
Compared with traditional cold runner injection molding, hot runner injection molding has obvious advantages. In traditional cold runner injection molding, after each injection molding, the plastic in the runner cools and solidifies, forming a large amount of agglomerated material. These agglomerated materials not only require labor and time for cleaning but also mostly cannot be directly reused in production, resulting in resource waste. Hot runner injection molding cleverly solves this problem, achieving efficient and smooth injection molding processes.
II. Significant Advantages, Reshaping Production Efficiency
Hot runner injection molding processing shows significant advantages in multiple aspects, comprehensively improving production efficiency.
Drastic Reduction in Material Costs
In traditional cold runner injection molding production, a large amount of plastic is trapped in the runner to form agglomerated materials. Especially for high-performance special plastics used in the aerospace field, the price is extremely high, reaching hundreds or even thousands of yuan per kilogram, and the waste cost caused by the agglomerated materials in the runner is astonishing. Hot runner injection molding technology eliminates the agglomerated materials in the cold runner and makes full use of the plastic. According to the actual production data of many enterprises, in the injection molding of products with complex structures and long runners, compared with traditional injection molding, hot runner injection molding can save materials by a proportion of 20%-50%, bringing considerable economic benefits.
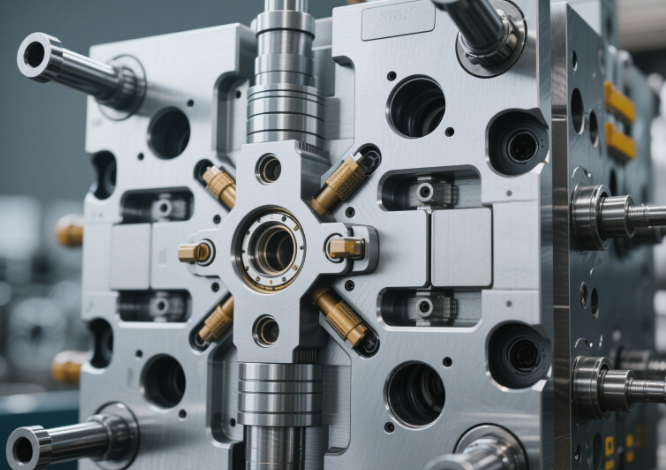
Leap in Production Efficiency
The hot runner system enables the plastic melt to fill the mold cavity more quickly, greatly shortening the product molding cycle. Taking the injection molding production of common electronic product casings as an example, before a well-known electronic manufacturing enterprise adopted the hot runner injection molding process, the molding cycle of a single mobile phone casing in traditional cold runner injection molding was about 30 seconds. After introducing the hot runner injection molding technology, it was shortened to about 20 seconds. Moreover, there is no need to clean the agglomerated materials in the cold runner, reducing the equipment downtime, and significantly improving the overall production efficiency, which can quickly respond to the large market demand in mass production.
Upgrade in Product Quality
With excellent temperature and pressure control capabilities, the hot runner system ensures the uniform distribution of the plastic melt within the runner. During the product molding process, it effectively reduces the probability of defects such as product deformation, warping, and weld lines. For example, in the injection molding production of automotive interior parts, automotive instrument panels have complex shapes and high requirements for appearance quality. After a large automotive parts manufacturer adopted the hot runner injection molding technology, it successfully solved the problems of deformation and surface weld lines that were prone to occur in the traditional injection molding process. The produced instrument panels have high dimensional accuracy and smooth surfaces, improving the overall quality of the products and their market competitiveness.
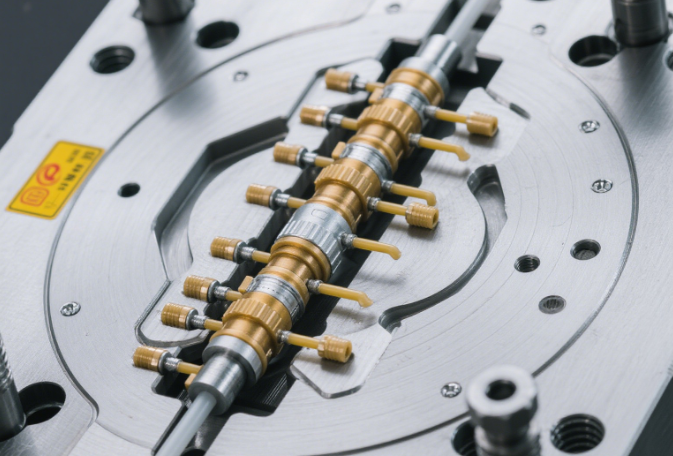
Win-win Situation of Reduced Equipment Wear and Energy Conservation
The plastic melt in the hot runner always maintains good fluidity, and the injection molding process can complete the mold filling action under lower injection pressure. The lower injection pressure reduces the wear on the mold and extends the service life of the mold. For example, for a large injection mold worth hundreds of thousands of yuan, after adopting the hot runner injection molding process, the maintenance cycle is extended from once every 3 months originally to once every 6 months, reducing the mold maintenance cost. At the same time, the lower pressure requirement reduces the energy consumption of the injection molding machine, achieving energy-saving operation. According to statistics, after large injection molding machines adopt the hot runner injection molding process, the energy consumption may be reduced by 10%-30%, saving a large amount of energy costs for enterprises in long-term production.
III. Diverse Applications, Covering Key Fields
Hot runner injection molding processing technology, with its own advantages, has been widely applied in multiple key fields.
Automotive Parts Manufacturing
The automotive industry has extremely strict requirements for the quality and performance of parts. Hot runner injection molding technology plays an important role in the production of large parts such as automotive bumpers, instrument panels, and door interior panels. Automotive bumpers need to have excellent strength and toughness to deal with collisions and also have good appearance flatness. A globally renowned automotive parts supplier adopted the hot runner injection molding process to produce automotive bumpers, precisely controlling the flow and molding process of the plastic melt. The produced bumpers meet the high-strength requirements, and the surface quality reaches extremely high standards. The high-efficiency production capacity also meets the mass production requirements of the automotive industry.
Production of Electronic and Electrical Products
In the field of electronic and electrical products, hot runner injection molding technology is crucial for the production of products such as mobile phone casings, computer keyboards, and charger casings. These products have strict requirements for dimensional accuracy and appearance quality. Taking the manufacturing of mobile phone casings as an example, high-precision dimensional control is required to ensure the perfect assembly of parts. A well-known mobile phone manufacturer adopted the hot runner injection molding technology to produce mobile phone casings, precisely controlling the flow of the plastic melt. The produced mobile phone casings have high dimensional accuracy and smooth and delicate surfaces, meeting the high requirements of consumers for product appearance and quality. Its high-efficiency production capacity also adapts to the characteristics of rapid product updates and large market demand in the electronic and electrical product industry.
Production of Packaging Containers
The production of packaging containers such as cosmetic packaging bottles and food packaging boxes has high requirements for the utilization rate of plastics and production efficiency. Hot runner injection molding technology can not only reduce plastic waste and production costs but also quickly produce packaging containers with exquisite appearance and precise dimensions. Taking cosmetic packaging bottles as an example, their appearance beauty directly affects the market attractiveness of products. A cosmetic packaging production enterprise adopted the hot runner injection molding technology, and the produced packaging bottles have smooth surfaces, high transparency, and precise dimensions, fully meeting the strict requirements of the cosmetics industry for packaging appearance and hygiene standards.
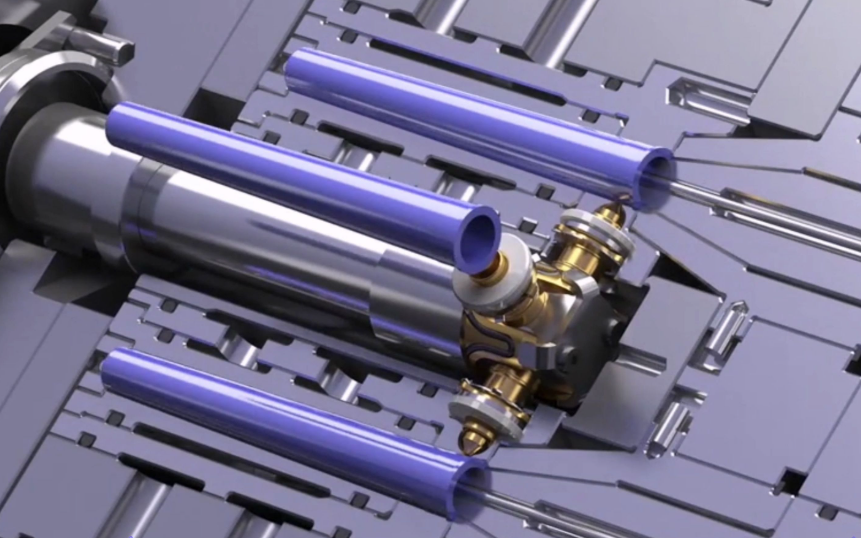
Medical Device Manufacturing
Medical device products have almost extremely strict requirements for quality and safety. Hot runner injection molding technology can be used to produce medical products such as syringes, infusion sets, and medicine bottles, ensuring high precision and stability of the products. Taking the production of medical syringes as an example, their dimensional accuracy is directly related to the accuracy of the injection dose, which is related to the life and health of patients. A professional medical device manufacturer adopted the hot runner injection molding technology, precisely controlling various parameters of the injection molding process. The produced medical syringes have extremely high dimensional accuracy, with the deviation controlled within a very small range, providing reliable plastic products for the medical industry.
Hot runner injection molding processing technology, with its innovation in technical principles, significant advantages, and wide application fields, is continuously promoting the plastic product production industry to move towards the direction of high efficiency, precision, and high quality, and has become an indispensable important force in modern manufacturing.
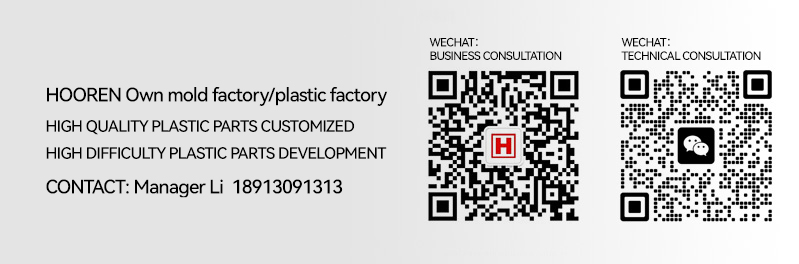